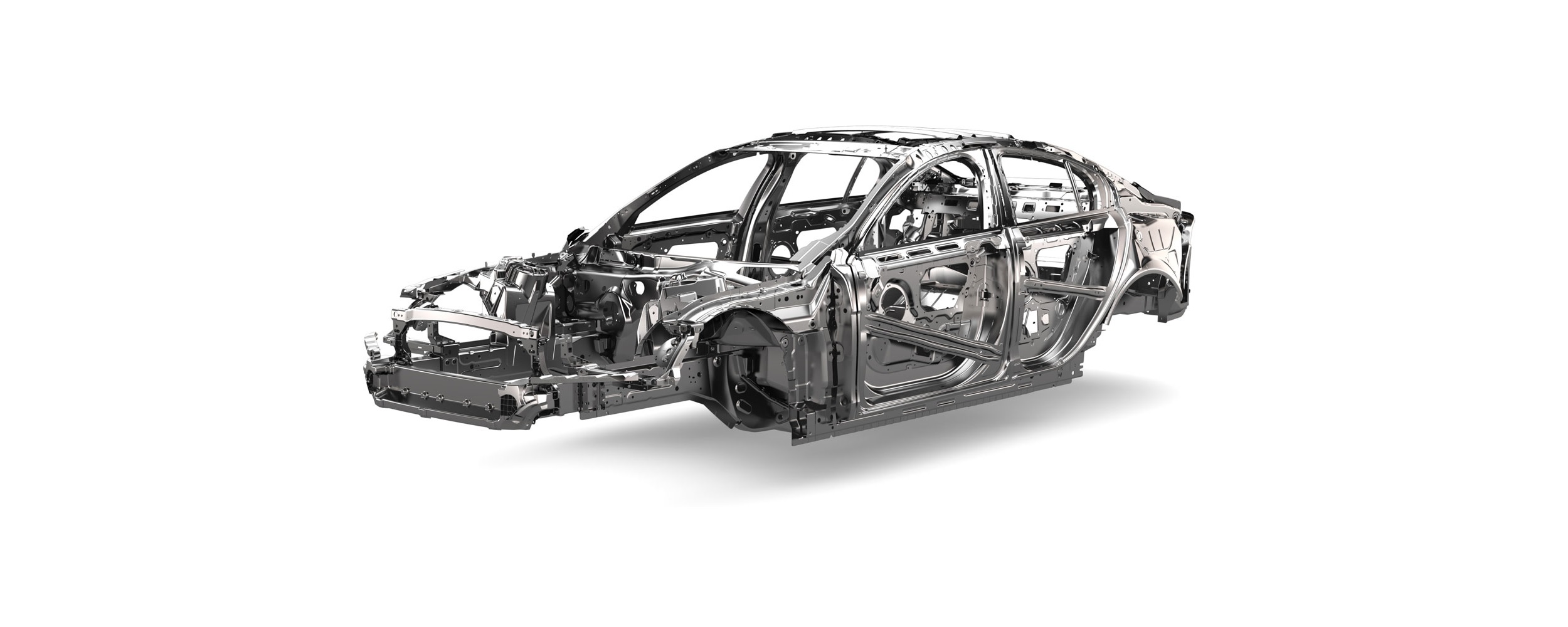
BIW装配与原型制造
简介
Car Bench在为汽车行业的OEM提供原型制造服务方面有着悠久的传统。
Protoline设备的核心应用之一是在白车身(BIW)部件的生产中。要利用现代化生产方法构建系统化的BIW装配流程,必须深入了解需要遵循的具体约束条件。以下概述了Car Bench系统在BIW装配中的商业优势。
车身构造方法
当前普遍使用的是传统固定焊接箱体构造技术,这种技术已被全球采用多年。
然而,它如今被视为车身构造中许多尺寸误差的来源。此外,在设计需要系统化夹紧移动或定位点调整时,这种方法难以调整或修改。
工装设置
传统系统 (BCM)
• 车辆设计完成后,由生产工程部门负责设计工装夹具,随后进行制造、组装和检查。
• 典型工装夹具设计和制造周期约为20周。
Car Bench灵活系统
• 车辆设计在进行的同时完成工装夹具设计,确保夹具在最终工程设计发布后数天内即可完成。
• 工装夹具最快可在4周内交付。
工程变更的工装调整
传统系统 (BCM)
• 调整难度大,需要对需要更改的部分进行重新加工或报废并重新制造。
Car Bench灵活系统
• 可在3D CAD系统中验证调整方案,确保准确无误。
空间需求
传统系统 (BCM)
• 工装夹具通常安装在固定位置,占用大量空间。
Car Bench灵活系统
• Car Bench系统可根据车辆生产需求灵活调整,占用空间较小,且可通过分步构建优化效率。
成本
传统系统 (BCM)
• 短期成本较低,因这类工装夹具通常在中国、印度或韩国制造,人工成本较低。
Car Bench灵活系统
• 初期投资适中,因为需要投资一套基础工装夹具。然而,从长期来看,由于工装调整可由装配人员现场完成,总成本更具竞争力。
质量
传统系统 (BCM)
• 工装夹具专为特定产品设计,不同供应商的标准可能导致质量不一致。
Car Bench灵活系统
• 每辆车均生成“主构建”,确保所有构建符合已知标准。
• 可在原型制造阶段开发和评估定位策略,为生产设施提供提前信息,同时无需额外成本尝试新策略。
使用寿命
传统系统 (BCM)
• 专用于特定项目和平台。
Car Bench灵活系统
• 支持多平台和项目使用,设备设计坚固耐用,项目结束后仍可继续使用数年。
• 零部件可替换或增加,例如因意外掉落导致的轻微损坏不会导致工装报废。
焊枪操作
传统系统 (BCM)
• 焊枪操作在工装设计时评估,若设计发生变化,通常需打磨夹具,甚至可能导致部件无法夹紧。
Car Bench灵活系统
• 提升焊枪可达性,设计时即可评估焊枪路径,必要时可移动支撑臂或柱体,同时保持正确夹紧或成型位置。
其他用途
传统系统 (BCM)
• 无额外用途,仅限于特定使用场景。
Car Bench灵活系统
• 可作为蓝模系统基础,在数据尚未充分时便可开始使用。该系统可随着平台变更和新项目重新利用,无需额外成本。
灵活系统的优势
• 全球统一夹具标准:所有开发项目遵循相同标准,确保平台和版本间的一致性。
• CAD设计夹具:与产品设计匹配,无需制造时间,仅需生产用户定义的界面部件,加快投产时间。
• 低修改成本:夹具调整成本最低,仅在形式变化时产生成本,夹紧位置修改不产生费用。
• 主构建的生成:确保每次构建符合已知标准,为生产设施提供提前信息,无需额外成本尝试新定位策略。
• 缩短设计与开发时间:让设计师专注于核心问题,减少后续工具更改成本。
• 平台适应性强:支持所有平台的已知构建条件,提供可追溯的构建历史记录,以满足客户需求(如碰撞和NVH)。
• 制造时间更短:相比传统方法显著减少。
• 经久耐用:该系统可持续使用30年或更长时间。
传统系统 (BCM) Car Bench灵活系统
传统系统 (BCM) Car Bench灵活系统